Abrasive blasting is another name for sandblasting. It involves applying high pressure while violently directing a stream of abrasive material on a surface to shape, roughen, smoothen, or remove pollutants from the surface. This method has many variations, including soda blasting, shot blasting, bead blasting, and sandblasting. Systems, gears, and parts used in sandblasting equipment project blast media against a part’s surface to scour, clean, or change the surface. Using compressed air, pressurized water, or a blast wheel, sand, abrasive material, metal shot, and other blast media are driven or propelled. Read More…
Our sandblast equipment is designed to handle a wide variety of applications and we use manufacturing methods that guarantee these machines will stand the test of time.

We have decades of experience in the finishing industry and we specialize in aqueous washing, abrasive blasting, vibratory finishing, polishing and buffing.
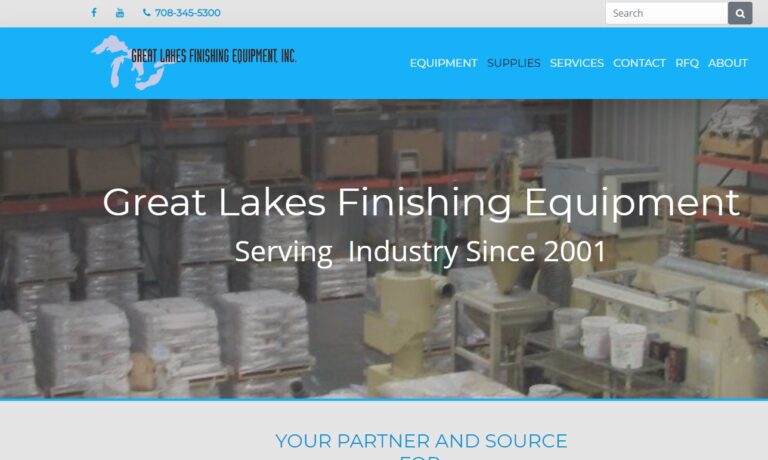
At Media Blast & Abrasives, Inc., we are dedicated to delivering exceptional sand blast equipment designed to meet the diverse needs of various industries. Our expertise centers on creating solutions that enhance efficiency and precision in surface preparation, whether for large-scale industrial applications or specialized, detailed projects.
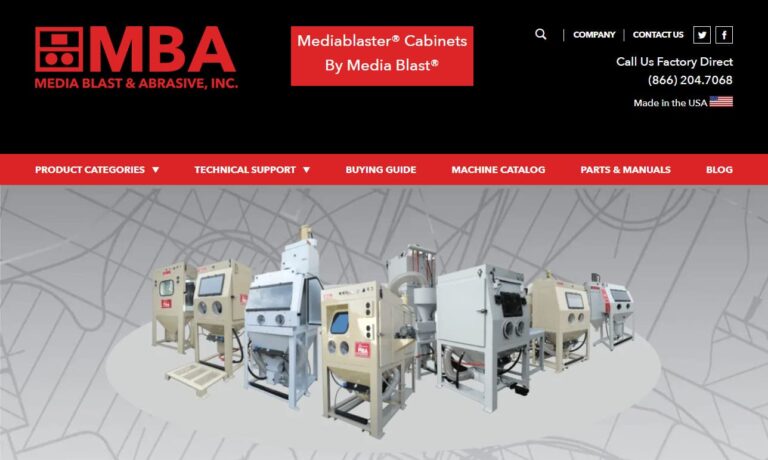
At IDS Blast Finishing, we are dedicated to delivering top-of-the-line sandblast equipment and abrasive solutions designed to meet the diverse needs of our customers. Our expertise in blast finishing enables us to provide robust and reliable solutions that ensure precise surface preparation and finishing for a wide array of industries.
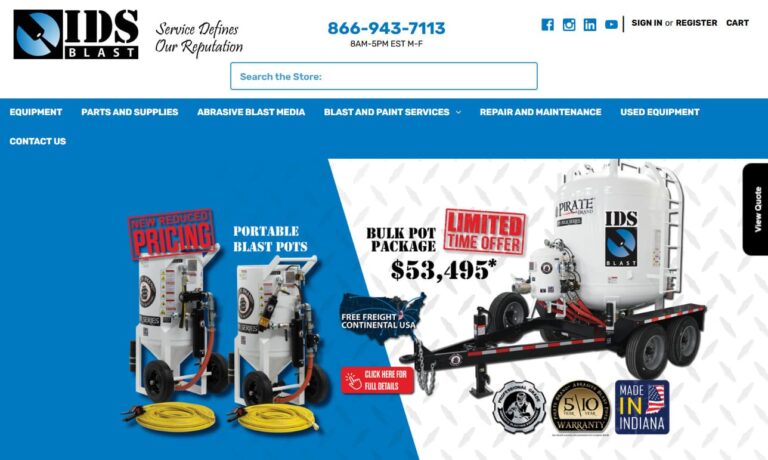
At Blast-It-All, we specialize in designing and manufacturing high-quality sandblasting equipment that meets the rigorous demands of industrial applications. Our commitment to innovation and craftsmanship drives us to engineer solutions that enhance surface preparation efficiency and deliver consistent, high-quality results. We offer an array of sandblasting equipment built to withstand...
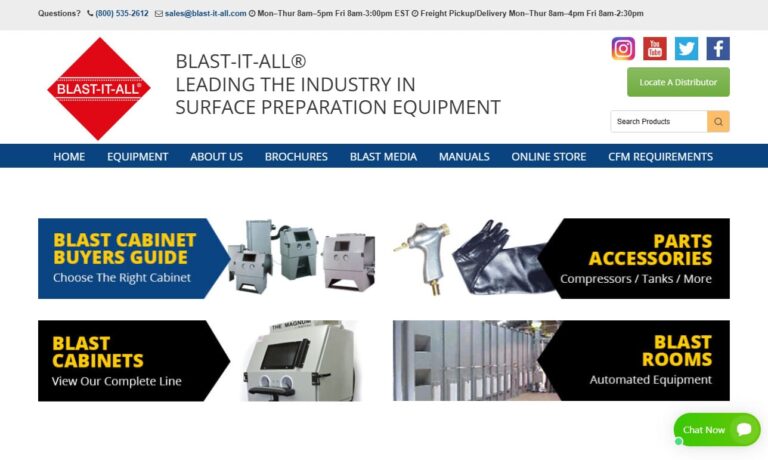
More Sandblasting Equipment Manufacturers

Types of Sandblasting Equipment
Vapor Blasting Equipment
Wet blasting, vapor honing, liquid honing, and dustless blasting are all used to describe vapor abrasive blasting. Using pressurized water and abrasive media removes impurities from surfaces during the wet blasting process. Since the water cushions the abrasive, vapor blasting is more delicate than dry blasting. Additionally, the water dampens the operation and collects the particles the abrasive removed. Additionally, wet blasting cushions the abrasive's impact, distributing it uniformly and in a feather-like pattern throughout the surface, enabling a finer blast technique.
Vapor sandblasters have a wider operating pressure range and more precise control of the wet abrasive blasting process than other blasters. Vapor abrasive blasting equipment can be used at pressures as low as 30 psi for paint removal to as high as 20,000 psi for white metal blasting for corrosion prevention.

Wheel Sandblasters
Centrifugal wheel blast technology is the foundation of another important category of sandblasting or shot-blasting equipment. A rotating turbine wheel impeller's axis receives blast media. The blast wheel accelerates and flings the shot or abrasive media onto the pieces using a series of throwing paddles or blades. The media stream can be directed to regulate the blast pattern and the size and position of the "hot spot" by adjusting the control cage surrounding the spinning blades. Depending on the size, speed, and distance between the wheel and part surfaces, the blast pattern can range in breadth from a few inches to several feet.
A section of the blasted surface, known as, “the hot spot,” gets heated to the touch. The hot spot indicates to the operator where the blast flow's center is. The most violent part of the blast media stream is called the hot spot. In other words, the hot zone has more hits per unit area. The operator changes the blast pattern to direct the hot spot onto the parts if they are not already warm to the touch.
Heavy blast media are perfect for movement, including cast shots, cut wire shots, steel shots, stainless steel shots, metal grit, and wheel blasters. Wheel blasters are often not used for blasting aluminum oxide or other angular abrasive material. A round steel shot works well for descaling forgings, cleaning castings, and shot-peening structural elements.

Slurry (Air Abrasive) Blasting Equipment
Slurry blasting is the technique whereby the abrasive material and water are combined and then pressured in a pressure pot before being pushed through the blast nozzle by compressed air. It is possible to convert dry blasting equipment to offer wet blasting. Air abrasive water blasters are another name for slurry blast devices. An air-blasting pistol is equipped with a water injection nozzle or water ring (halo), which adds water to the blast media stream. As a result, they reduce the dust produced by 50% to 85%. However, the water ring or halo nozzles are less effective in controlling dust than water induction or injection nozzles.
Because they can wet blast, dry blast, rinse, and dry parts, slurry blasters are quite versatile. Cleaning up the muddy mess left behind by slurry blasters in field applications is one disadvantage. The big water hose and the slurry blast equipment make it difficult for the operator to carry and manage.
Applications of Sandblasting Equipment
- Before welding, adhesive bonding, and painting, automobile OEM, abrasive blasting equipment is used to clean, etch, and prepare the surface of the parts. Shot peening is used to strengthen and lengthen the life of several castings, forgings, and machine parts.
- According to the automotive aftermarket, sandblasters are crucial tools in auto body and vehicle repair shops. They are used to remove auto body corrosion, do body and engine repairs, and restore vintage vehicles.
- The anchor profile generation and surface cleaning boost the bond strength of adhesives and sealants.
- Sandblasting is used in architecture and building construction to take paint and rust off steel, concrete, and wooden structures. For cleaning and deodorizing fire, smoke, and mold damage, as well as for graffiti removal, paint stripping, and other architectural cleaning tasks, sandblasters are becoming more and more popular.
- Brick, stone, and concrete walls can be cleaned with vertical sandblasters. Concrete floors are cleaned with walk-behind sandblasters before being recoated. An inbuilt vacuum system is frequently included with vertical and walk-behind blasters to collect blast material and dust.
Choosing the Proper Sandblasting Equipment Supplier
To make sure you have the most productive outcome when purchasing sandblasting equipment from a sandblasting equipment supplier, it is important to compare at least 4 suppliers using our list of sandblasting equipment companies. Each sandblasting equipment supplier has a business profile page that highlights their areas of experience and capabilities and a contact form to directly communicate with the supplier for more information or request a quote. Review each sandblasting equipment business website using our proprietary website previewer to get an idea of what each company specializes in, and then use our simple RFQ form to contact multiple sandblasting equipment companies with the same quote.